IO-Link
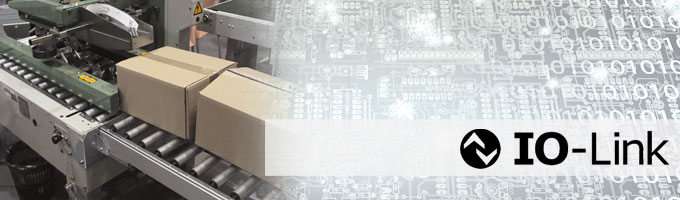
What is IO-Link?
Most sensors and actuators today are already equipped with microprocessors, which can be used for parameterization, storing configuration data, and controlling indication. The obvious next step is to overcome the bottleneck of the binary standard interface and make additional functions centrally accessible for the automation system.
For this reason a lot of well-known manufacturers from the field of automation have come together and developed a fieldbus independent communication interface for sensors and actuators:
IO-Link.
Compatibility with existing technologies was the primary objective during development in order to guarantee investment protection.
Technology
IO-Link is based on a point-to-point connection between the sensor/actuator and an interface module. Up to now, the binary connection was only designed for transferring switching information, but IO-Link now allows two bytes to be transferred normally in a 2 ms cycle via a combined switching status and data channel. Other information can be exchanged in addition to the process values, such as parameters or diagnostics messages. This enables communication with sensors and actuators down to the “last meter” to be established for universal communication.
Integration in Profinet systems
IO-Link devices could so far not be directly integrated in Profinet projects. Users were commonly forced to enter properties such as device class or manufacturer ID manually. Parameters such as measuring ranges and output signals had to be programmed or set via additional software.
Turck now provides help with a new function. SIDI (Simple IO-Link Device Integration) enables IO-Link devices to be integrated directly in a Profinet engineering software such as the TIA Portal. IO-Link devices are entered here as Profinet submodules in the GSDML (Generic Station Description Markup Language) of the IO-Link masters. As a standard feature, Turck adds all its proprietary IO-Link devices to the SIDI library, as well as the devices of its strategic partner for optical sensors, Banner Engineering.
If the connected device is in the SIDI GSDML, PLC programmers can select it from the device catalog in their programming environment. The programmer can view all the relevant IO-Link properties for these devices and alter parameters, such as measuring ranges, output signals or pulse rates in the plain text field. Offline engineering is therefore also entirely possible with IO-Link devices.
IO-Link is Opening the Door to Industrial Internet of Things
Further Information
- Whitepaper – IO-Link as an Information Channel for Condition Monitoring
- Manual – IO-Link-Devices – Commissioning
- Video – IO-Link is Opening the Door to Industrial Internet of Things
- Brochure – IO-Link All-in-One Solutions – Enabler for Industry 4.0
- Flyer – IO-Link – Simple, Seamless, Efficient
- Flyer – TBEN-L | TBEN-S | TBPN – Multiprotocol I/O Modules with IO-Link Master
- Technical Article – Powerful Duo for IIOT – more12005e [PDF, 0,73 MB]
- Technical Article – Naturalized – more11971e [PDF, 0,39 MB]
- Technical Article – Planning with Foresight – more21705e [PDF, 0,40 MB]
- Technical Article – IO-Link Series Growing – more21505e [PDF, 0,60 MB]
- Topics & Technologies
- Asset Monitoring Gateway with Cloud ID
- Asset Monitoring Gateway with SNAP ID
- Codesys
- Condition Monitoring
- Ethernet in Hazardous Locations
- Field Logic Controller
- Industrial Cloud
- Industry 4.0
- IO-Link
- Machine Safety
- Modular Machines
- Module Type Package
- Multiprotocol Ethernet
- Pick-to-Light
- Profinet
- RFID
- Safe work and Occupancy Monitoring
- Snap Signal
- Sustainability
- TAS – IIoT Service Platform
- The Visual Factory